Environmental Aging
The laboratory has strong expertise in the environmental durability of civil engineering elements (corrosion of steel, aging of polymers and composites, etc.). Therefore, the laboratory has numerous dedicated installations and devices to understand the coupling between mechanical stress and environmental aging.
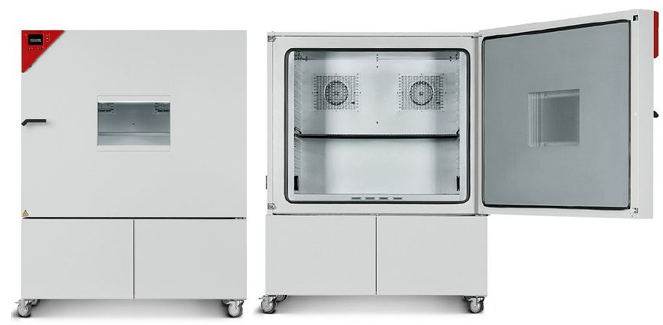
Thermohygrostat chambers
The laboratory has two thermohygrostat chambers (MKF 720 and KMF 720 models) that enable it to carry out investigations (aging, cycling, creep, etc.) in a controlled environment of temperature and humidity.
One of the chambers allows for rapid temperature changes with humidity regulation (-40 to 180°C, 10 to 98% RH). The second chamber provides perfectly constant and homogeneous conditions in temperature and humidity (-10 to 100°C; 10 to 98% RH).

Cyclic corrosion testing chambers
The laboratory has two cyclic corrosion testing chambers (models S1000XP and CC1000ip). Both chambers can recreate 3 distinct climates (salt spray, saturated humidity/condensation, air drying). The CC1000ip chamber also allows for creating a controlled humidity climate.
The salt spray test can be performed from ambient temperature up to +50°C, drying from ambient temperature up to +70°C, and controlled humidity from 25% RH at 30°C to 85% RH at 60°C. These climates can be programmed to occur in any order and repeat automatically.
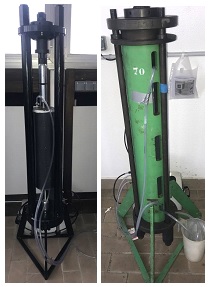
Stress corrosion aging in distilled water
The stress corrosion aging of metallic reinforcement bars in distilled water consists in subjecting them to a constant load while aging them in a circulating cell (with a splash zone) filled with distilled water. These tests are carried out in accordance with standard NF A 05-30. After being aged for 3 months, the reinforcement bars are subjected to a tensile test to determine their residual mechanical characteristics. The laboratory has several dedicated setups and cells for these investigations.
These setups are also used to study the aging under load of composite reinforcement bars in alkaline solutions at different temperatures.
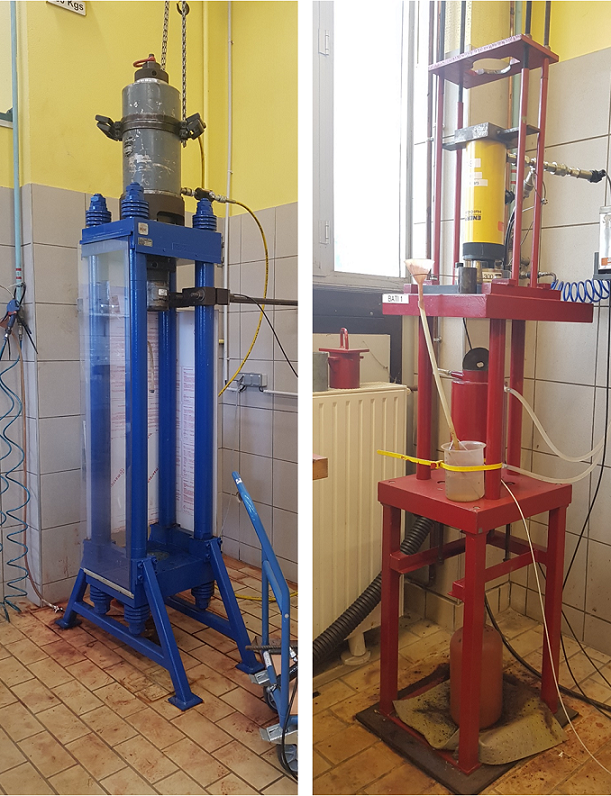
Stress corrosion aging tests (ammonium thiocyanate)
The stress corrosion aging of metallic reinforcements refers to the process by which metals undergo structural degradation and modifications of their mechanical properties due to the combination of factors such as stress, temperature, and exposure environment. These three factors are implemented in the tests conducted in the laboratory as part of stress corrosion tests in an ammonium thiocyanate solution provided in paragraph 11 of standard NF EN ISO 15630-3.
Mechanically, aging results in a loss of ductility and an increase in the stiffness of the steel, which makes structures more brittle and more prone to corrosion and cracks. The SMC laboratory has three stress corrosion testing facilities with ammonium thiocyanate, two designed to accommodate prestressing wires and strands and one designed to accommodate prestressing bars. Each of these facilities has a loading device (hydraulic cylinders and power units), a force sensor (200kN, 300kN, or 1200kN), and a temperature control device for the solution.
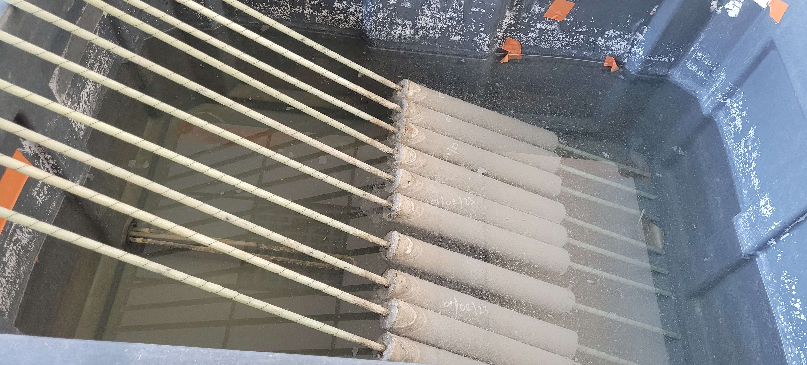
Thermostatic tanks
The study of the durability of civil engineering materials requires us to recreate laboratory conditions that are as close as possible to the real environment. To do this, the laboratory has several thermostatic tanks filled with solutions in which different samples are immersed.
The solutions can be of various types:
seawater
fresh water
solution simulating the "concrete" environment (pH>10)
It is also possible to recreate conditions of tidal range, splash zone, and accelerate phenomena by heating the solution up to 60°C.
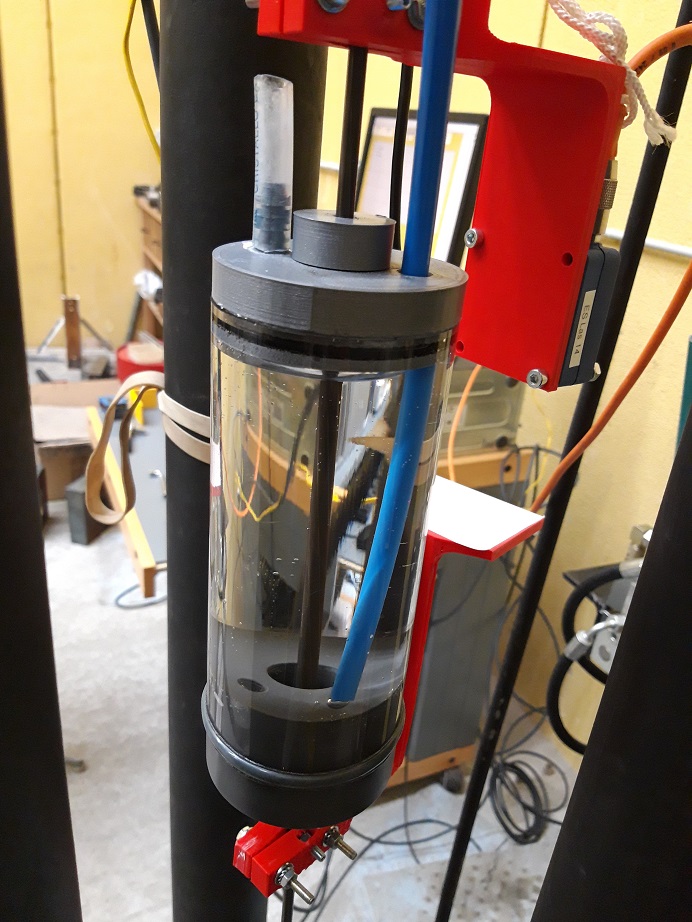
Slow strain rate test
Slow strain rate test involves applying a dynamic strain to the specimen in the presence of a corrosive environment at a very low strain rate, typically between 10-5 and 10-7 s-1. Although it is further from the actual service conditions, it is more discriminative and allows us to measure mechanical parameters such as Rm, Agt, or elongation and compare various aggressive environments.
The main advantage, however, is the acceleration of the corrosion rate. Indeed, the application of strain to the specimen creates a renewal of the metal surface (depassivation) and thus significantly increases the harmfulness of the corrosive solution on the specimen.